Hardcore Innovation: GU HS Series Gantry Machining Center
2024-07-25
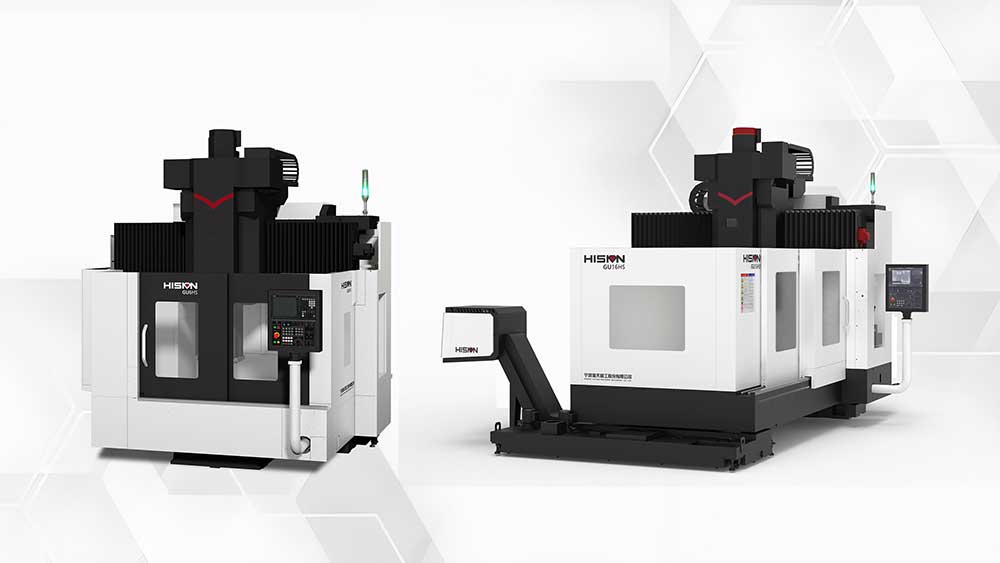
The GU HS Series Gantry Machining Center from Haitian Precision embodies the traditional gantry features of strong rigidity, symmetrical structure, and high stability, offering a variety of specifications to meet market demands with table widths ranging from 700mm to 1500mm. This series further highlights the advantages over traditional C-type vertical machining centers, enhancing cutting performance and providing a new experience for customers. The product is suitable for fields such as construction machinery, automotive parts, molds, and plastic machinery. Its exceptional chip rigidity, efficient metal removal rate, and stable and reliable machining accuracy are its core strengths.
Expanded Machining Range? The Z-axis travel of the entire GU HS series has been increased to 800mm, and both the gantry width and Y-axis travel have been enhanced.
Powerful Cutting Capability? The entire series is equipped with high-rigidity cross hard rail rams, ensuring the rigidity and anti-vibration needed to fully utilize the high-torque performance. The integrated structure of the beam and column reduces contact surfaces and error accumulation, enhancing reliability and stability.
All transmission components are self-made, with a full-gear transmission gearbox for quick and convenient shifting, smooth rotation, and low noise.
Haitian Precision’s self-developed high-torque mechanical spindle offers a maximum speed of 6000rpm, a maximum torque of 520Nm, and a 6+1 bearing arrangement, ensuring strong cutting without vibration, suitable for heavy-duty machining. The spindle features a mechanical safety lock for safer tool changes.
Rich Optional Features? The HS ram is pre-equipped with an automatic head interface. In addition to the manually adjustable head, it also offers an optional BT50 automatic right-angle head.
Intelligent Module Upgrades? Secondary development of the system software makes the product smarter, with features like parameterized workpiece adaptive function, visualized tool load monitoring, simplified processing condition selection, and digitized operation monitoring. Additionally, a spindle thermal compensation function can be added to ensure stable machining accuracy.
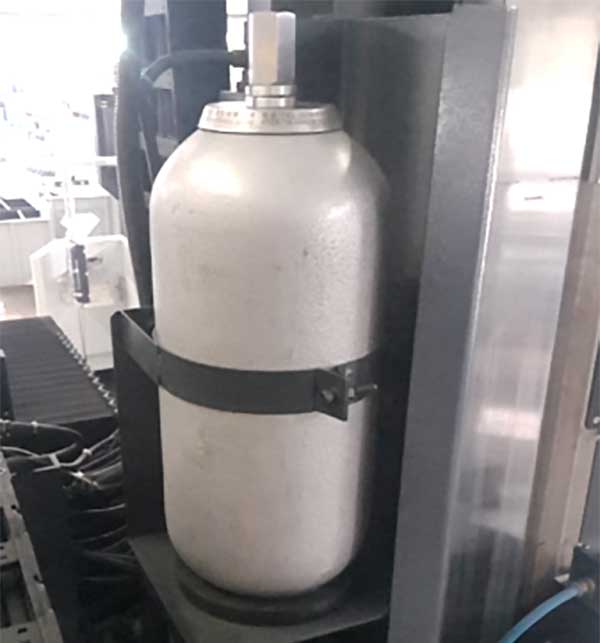
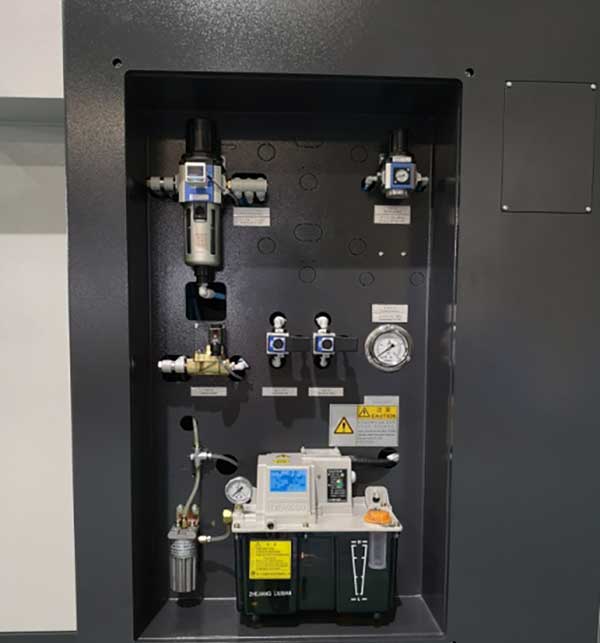
Flexible Automated Production Line? ?The main machine offers a wide range of automated production line configuration options, suitable for producing various parts from small batches to medium-large batches, making factory automation easy to achieve.
Heavy Cutting (Cast Iron)
Tool: Φ125 Face Mill
Material: HT200
Speed: 450rpm
Cutting Width: 100mm
Cutting Depth: 8mm
Feed Rate: 800mm/min
Tapping (Cast Iron)
Tool: M42x2 Fine Thread Tap
Material: HT200
Speed: 150rpm
Cutting Width: 2mm
Cutting Depth: 65mm
Feed Rate: 300mm/min
Heavy Cutting (Steel)
Tool: Φ125 Face Mill
Material: 45#
Speed: 450rpm
Cutting Width: 100mm
Cutting Depth: 6mm
Feed Rate: 783mm/min
Tapping (Steel)
Tool: M42 Coarse Thread Tap
Material: 45#
Speed: 114rpm
Cutting Width: 4.5mm
Cutting Depth: 65mm
Feed Rate: 513mm/min
Heavy Drilling (Steel)?
Tool: U98 Drill
Material: 45#
Speed: 330rpm
Cutting Width: 98mm
Cutting Depth: 150mm
Feed Rate: 50mm/min
Boring (Cast Iron)
Tool: Φ320 Boring Tool
Material: HT200
Speed: 200rpm
Cutting Width: 8mm
Cutting Depth: 80mm
Feed Rate: 40mm/min
Boring (Steel)?
Tool: Φ320 Boring Tool
Material: 45#
Speed: 200rpm
Cutting Width: 6mm
Cutting Depth: 80mm
Feed Rate: 32mm/min